Fiberglass auto body repair has entered a new era. Technological advancements are reshaping the repair process. Precision tools and advanced materials are now widely used. The goal is to restore form and function with minimal compromise.
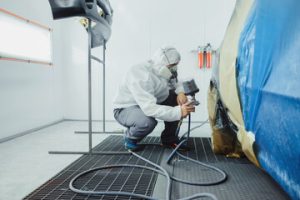
Modern repairs begin with structural analysis. Repair technicians now scan the panel using digital imaging. This creates a visual map of cracks, stress points, and voids. It improves planning and prevents overworking the surface. Keep reading the article below to Learn More.
Surface integrity is critical in fiberglass repair. Microscopic inspections detect air pockets and fiber separation. Identifying these early avoids future delamination. Repairs now aim to be both cosmetic and structural.
New resin blends are making repairs stronger. These resins offer better flexibility without sacrificing bond strength. They also reduce curing time and shrinkage. As a result, panels retain their shape after hardening.
Smart curing methods are improving consistency. Heat-controlled environments reduce environmental errors. UV-assisted curing is also becoming more common. These methods ensure faster and more predictable outcomes.
Sanding technology is evolving with new materials. Abrasives now target only the necessary layers. This minimizes collateral damage to surrounding areas. Technicians can now work faster and with more accuracy.
Panel reshaping tools are gaining popularity. They restore original curves without adding unnecessary filler. Templates and guides assist with contour matching. The outcome is a seamless surface that needs little correction.
Color-matching in fiberglass repair has improved through software. Paint formulas are digitally aligned with existing coats. This reduces rework caused by slight mismatches. Repairs now blend naturally into the original finish.
Dust extraction systems are being upgraded in workshops. These keep particles away from sensitive repair zones. Clean surfaces improve adhesion and final aesthetics. It also protects workers from airborne fibers during sanding.
New fillers for fiberglass are lighter and more elastic. They follow panel movement during temperature changes. This flexibility reduces cracks caused by stress. Repaired panels last longer and stay visually intact.
Educational training has been updated to include material science. Repair technicians study fiberglass composition and stress behavior. This knowledge informs better application of repair materials. It also shortens the learning curve for advanced repairs.
Laser-guided measurements are now standard in complex repairs. They track panel alignment during reassembly. This helps restore symmetry after significant damage. Repairs are now more than patchwork—they restore original engineering.
Customized fiberglass sheets are being produced for patching. These pre-measured mats match different car body types. It reduces trimming and shaping work on site. Technicians spend more time bonding and less time prepping.
Low-pressure vacuum systems assist in resin application. They prevent air pockets from forming during hardening. This improves strength and finish quality. The method is now used in both minor and major repairs.
Weather-resilient coatings are applied to repaired areas. These coatings protect against UV damage and moisture. They extend the durability of both old and new sections. Repaired vehicles now have longer surface integrity in varying climates.
Thermal imaging helps identify underlying damage. Even if a panel looks fine, heat mapping shows inconsistencies. Technicians then target those weak areas first. This reduces repeat repairs and surprises after delivery.
Reinforced mesh inserts are used for structural enhancement. These meshes support panels without adding weight. They distribute impact force in case of future accidents. Repairs now anticipate future risks, not just present flaws.
Workshop lighting is changing to highlight imperfections. Color-corrected lights help identify fiber distortion. They also reveal missed sanding or uneven filler. Better visibility leads to cleaner and more consistent finishes.
Mobile apps now document the repair process step by step. Customers receive visual updates of progress and techniques. This adds transparency and builds trust in services. Digital records also help track repair history over time.
Greener resin options are reducing environmental impact. Some are derived from renewable sources or produce less waste. Fiberglass repair is becoming part of the sustainability movement. Eco-conscious customers are now a key market.
Weather modeling influences when outdoor repairs are scheduled. Sudden shifts in humidity can ruin resin bonding. Apps now guide technicians on optimal working windows. This ensures better results with fewer environmental risks.
Denting and warping are now countered with memory-mold technology. These tools help return panels to their exact factory curve. They reduce guesswork and manual manipulation. This keeps design lines clean and proportional.
Welding is being replaced in certain areas with high-bond epoxy. This adhesive rivals metal joints in strength. It allows clean repairs on fiberglass without heat. Delicate areas are now fixed without risk of deformation.
Time-efficient layering techniques are improving productivity. Alternating thin resin and mat layers build strength rapidly. This technique reduces bulk and sagging. Repairs look natural and function like the original panel.
Precision cutting machines shape fiberglass with minimal error. CNC-style tools are adapted for composite materials. They reduce waste and speed up patch preparation. These machines are ideal for high-volume or repeat repairs.
Humidity control is now a standard part of repair environments. Excess moisture affects resin bonding and curing speed. Climate-controlled booths create the perfect repair zone. This ensures uniformity across different repair projects.
Virtual reality simulations train new technicians faster. These programs replicate real repair challenges. Trainees gain confidence before handling actual tools. This boosts workshop readiness without risk to real vehicles.
Automated inspection tools verify repair success. Lasers, sensors, and AI programs check panel smoothness and bond quality. Any inconsistencies are flagged immediately. This improves workshop quality control with minimal manual checking.
Flexible fiberglass sheets are expanding creative repair options. These sheets adapt to tighter curves and complex shapes. It allows more ambitious restorations with fewer cuts. Repairs now restore original styling without limitation.
Clear-coat technologies are evolving for better surface gloss. New formulas resist yellowing and provide UV defense. These coats also enhance color depth and realism. Repaired sections blend better and retain their look longer.
Recyclable fiberglass products are being developed for repair waste. Offcuts and failed patches are now repurposed. Workshops aim for near-zero material disposal. Repair work is aligning with long-term waste reduction goals.
Custom decals are being used to cover minor visual imperfections. These aren’t just decorative but also functional. They protect the repair site and match vehicle themes. Customers appreciate both form and function in one solution.
Ergonomic tool design reduces technician fatigue. Tools are lighter and shaped for natural grip. This allows better control during detailed fiberglass work. Precision improves as effort becomes easier to sustain.
Mobile fiberglass repair units are gaining traction. These units allow technicians to perform quality work on-site. Customers benefit from speed and convenience. Remote workstations now offer results once exclusive to full shops.
Augmented reality is used to overlay repair plans on the panel. Technicians see guides as they work in real time. This ensures accurate patch size, resin spread, and sanding zones. Mistakes are reduced and output consistency improves.
Insurance companies are updating policies for fiberglass repairs. Claims now consider eco-friendly and tech-based methods. This shift encourages modern approaches in damage repair. Customers gain more options and flexible coverage.
Digital templates assist in creating custom patch shapes. These templates are adjusted on-screen before cutting. This helps reduce waste and improves visual results. Repairs now involve design precision before physical work begins.
As fiberglass becomes more common in vehicle designs, repair methods must evolve. Tools, materials, and mindsets are shifting. Quality, speed, and sustainability are all valued in modern repairs. This new era of fiberglass repair blends technology with craftsmanship.